Industrial Wastewater Treatment Systems: challenges, solutions and practical approach
The treatment of industrial wastewater is a real “technological labyrinth”: it is not enough to comply with increasingly stringent regulations, but it is also necessary to streamline processes, cut costs and – when possible – transform water into a secondary resource.
Let’s start, however, from a firm point: what follows is the result of our experience, of the field tests and real case studies that we have supported our clients with. It is not a bible, but a practical handbook for orienting oneself among solutions, advantages and compromises.
With this guide, designed for plant managers, engineers and environmental consultants, we try to offer…
- Optimization and savings. Strategies to reduce OPEX and CAPEX: from water recovery (recycling, not throwing it away) to the modular “plug-and-play” solutions that we have experimented with.
- “Tailor-made” solutions. Because, unlike domestic wastewater, industrial wastewater changes from company to company (and even from line to line). Here you will find our approach: installation of an onsite pilot and analysis of real data, to define the most effective technology.
- Regulatory and operational clarity. A summary of the most relevant laws and standards (at national and EU level), accompanied by the advice we have gained in the field to avoid sanctions and unforeseen events.
1. Why is the treatment of industrial wastewater essential?
Before delving into the technologies, a reminder: these points arise from our case studies and pilot tests, not from universal dogmas. That said, here’s why we can’t do without it:
- Regulatory compliance. National and EU laws impose strict limits on discharge into sewers, rivers and soil. In case of non-compliance, you risk heavy fines and damage to the company’s image.
- Environmental protection. Any untreated effluent potentially causes damage to rivers and lakes: it alters the biological balance and pollutes vital resources.
- Operational efficiency and savings. Good treatment reduces disposal costs and often allows for the reuse of water (for cooling, internal washing…), with concrete savings.
- Corporate social responsibility (CSR). A green approach to water improves the reputation towards customers, investors and stakeholders.
- Fault prevention. Oils, greases and suspended solids can block pipes or damage pumps. Treating them correctly means avoiding plant downtime and costly repairs.
2. Common challenges in industrial wastewater treatment
Each industrial effluent has a different composition and consequently requires a “mix” of specific treatments. The most frequent difficulties are:
- Heterogeneous pollutants: from coarse solids to molecules, metals, solvents, colorants… a wide variety of nutrients.
- Variable flows and concentrations: production cycles, seasonality (e.g. food industry) or extraordinary events can cause loads and flow rates to fluctuate.
- Toxic or inhibitory substances: certain compounds also represent a danger for the bacteria involved in biological treatments, requiring targeted pre-treatments.
- Limited plant space: often the plants must be installed in limited square meters. Compact and modular solutions become key.
- CAPEX-OPEX balance: the investment must guarantee purification performance and economic sustainability.
- Constantly evolving regulations: discharge limits can become stricter within a few years. Providing for “built-in” upgrades is a must.
3. Fundamental parameters and key pollutants
Analyzing the effluent is only the first step. Below are the main parameters with a quick look at possible technological solutions based on our case studies (but not determinable in absolute terms).
- Total Suspended Solids (TSS). They represent the particles in suspension (organic and inorganic). If in too high a quantity, they clog and reduce efficiency. MITA use cases: lamella pack decanters for large loads, cloth or sand filters for finishing.
- BOD and COD. BOD measures the oxygen consumed by microorganisms in 5 days at 20°C; COD measures what is necessary to chemically oxidize the polluting substances present in a water sample (organic and inorganic). A high BOD/COD ratio indicates good biodegradability. MITA use cases: biodiscs and Biocombi systems for biodegradable material.
- Nitrogen (N) and Phosphorus (P). Too much nitrogen (NH₄⁺, NO₂⁻, NO₃⁻) and phosphorus (orthophosphates) favor eutrophication. MITA use cases: biodiscs configured for nitrification and anoxic stages for denitrification; chemical dephosphatation with iron/aluminum salts followed by sedimentation or filtration.
- Oils and greases. Common in the food, mechanical and petrochemical industries. They can be floating, emulsified or dissolved. MITA use cases: lamella pack oil separators or DAF flotators as pre-treatment.
- pH. Extreme values (acidic or basic) can be corrosive and biological inhibitors. Neutralization is needed before the main treatments.
- Heavy metals. Chromium, nickel, lead, cadmium, mercury… are removed by precipitation (pH variation), adsorption or ion exchange.
- Specific contaminants. Solvents, pesticides, phenols, colorants, surfactants… require a mix of technologies (physical, chemical and biological) calibrated following a pilot test.
Remember: each plant, and the mix of its effluent, remains a case in itself and deserves a dedicated analysis.
4. Overview of treatment technologies: the example of municipal wastewater treatment plants
The treatment process of civil wastewater develops in consecutive phases, each with a precise task within the municipal purifier. In the case of industrial wastewater treatment, as we have seen, the discourse is different: each plant responds to a different type of effluent and uses a different mix of technologies.
It is however useful to take the case of the municipal purifier as an example to see what the typical steps of wastewater treatment would ideally be (to then return to the industrial application).
- Pre-treatments. They remove what is “large” or harmful before moving on to the subsequent phases:
- Screening: removes suspended and floating solids from the wastewater before they enter a purification plant. It has a primary purpose of “protecting” the subsequent equipment.
- Grit and grease removal: separates sand, gravel and floating oils.
- Primary treatments. They deal with suspended solids and part of the organic matter:
- Sedimentation: the heavy solids “fall” by gravity. MITA WT technologies in this area: lamella pack decanters.
- Flotation: a process that produces micro-bubbles of air, which adhere to oils, greases and light particles, bringing them to the surface. MITA WT technologies in this area: dissolved air flotators.
- Secondary (biological) treatments. The microorganisms degrade the organic load and—in special configurations—nutrients such as N and P:
- Activated sludge: aerated tanks, simple but energy-intensive.
- Attached biomass: fixed or mobile supports; here the protagonists:
- Rotating Biological Contactor (Biodiscs): rotating discs, low consumption and reduced sludge. MITA WT technologies in this area: Biorulli® systems for biological treatments.
- MBBR – moving bed biofilm reactors: free plastic bio-supports in the tank.
- MBR: biological process + membrane for ultra-pure effluent.
- Tertiary treatments (finishing). They refine the effluent for stricter limits or reuse:
- Sand. MITA WT technology in this area: continuous sand filters (self-cleaning).
- Cloth. MITA WT technology in this area: free-fiber cloth filters.
- Disinfection: UV, chlorine, ozone.
- Advanced treatments.
- AOPs (advanced oxidation),
- nanofiltration,
- reverse osmosis.
The choice is not “one-size-fits-all”: it depends on the effluent, space, regulations, CAPEX/OPEX and reuse objectives.
Ask for Information5. Specific Applications for the Industrial Sector (focus on MITA solutions)
Each industrial sector has its own peculiarities. Below are some examples based on the experience of MITA Water Technologies. However, we always remember that each case must be evaluated individually, preferably with a pilot test.
5.1. Wastewater Treatment for the Food Industry
Characteristics of the effluent: high organic load (BOD, COD), presence of suspended solids, fats, sugars, proteins. A strong seasonal variability is often found (e.g. wineries, canneries).
Requirements: reduction of organic substance, removal of solids and fats.
MITA WT Wastewater treatment tecnologies
- Rotating Biological Contactors (Biodiscs): ideal for treating biodegradable organic loads. Their modularity allows them to adapt to production peaks (e.g. harvest for wineries). Simple to manage and with low energy consumption.
- Dissolved Air Flotators (DAF): excellent as a pre-treatment to remove fats and suspended solids, protecting the subsequent stages. Often crucial for dairies, salami factories, confectionery industries.
- Biocombi Compact Plants: “all-in-one” solution for small and medium-sized food companies, combining biological treatment (biodiscs) and final filtration (cloth) in a single system.
- Pile Cloth Filters: as a finishing touch to ensure compliance with restrictive discharge limits on suspended solids.
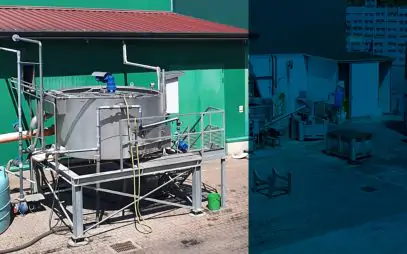
Application: Food Industry
Read the article and find out how we can support you5.2. Wastewater Treatment for the Textile Industry
Characteristics of the effluent: high water consumption, presence of colorants, surfactants, oils, greases, suspended solids (fibers), metals.
Requirements: color removal (often complex), COD and surfactant reduction, solids removal.
MITA WT Wastewater treatment tecnologies
- Rotating Biological Contactors (Biodiscs): effective in the reduction of surfactants and part of the organic load. Low electricity consumption is a plus for energy-intensive sectors.
- Dissolved Air Flotators (DAF): useful for removing suspended solids, oils, greases and a first reduction of surfactants, in addition to a partial removal of color if associated with particulate matter.
- Pile Cloth Filters / Continuous Sand Filters: for the final removal of suspended solids.
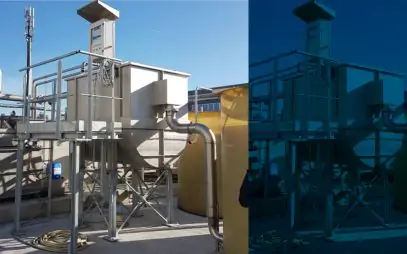
Application: Textile Industry
Read the article and find out how we can support you5.3. Water Treatment for the Plastics Industry
Characteristics of the effluent: presence of microplastics, fine solids, polymer residues, sometimes solvents or additives.
Requirements: accurate removal of fine suspended solids.
MITA WT Wastewater treatment tecnologies
- Pile Cloth Filters (in free fiber or microfiber): efficiency in the final stage removal of solids (less than 10 mg/l in output) and an economic life cycle, thanks to gravity filtration.
- Continuous Sand Filters: an efficient alternative for filtration, especially if continuous and robust operation is required.
Possible pre-treatments (e.g. sedimentation with lamella decanters) may be necessary in case of higher solid loads.
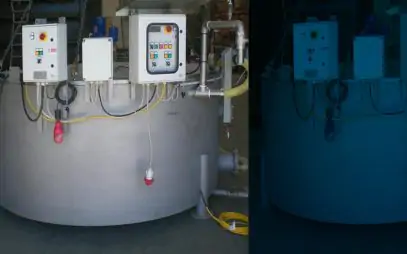
Application: Plastics Industry
Read the article and find out how we can support you5.4. Water Treatment for the Metals Industry
Characteristics of the effluent: presence of dissolved or suspended heavy metals, oils, acids/alkalis, solids. It varies greatly depending on the process (foundries, steel mills, surface treatments).
Requirements: removal of metals, pH neutralization, removal of oils and solids.
MITA WT Wastewater treatment tecnologies
- Lamella Pack Decanters: used to accelerate the sedimentation of metal hydroxides formed after pH adjustment (chemical precipitation).
- Pile Cloth Filters and Continuous Sand Filters: tertiary filtration systems with different operation but equally efficient.
- Lamella Pack Oil Separators: for the removal of oils from mechanical processing or cooling.
5.5. Water Treatment for the Oil & Gas Sector
Characteristics of the effluent: presence of oils (free, emulsified, dissolved), hydrocarbons, phenols, suspended solids, salts. Process water, washing water, stormwater from contaminated areas.
Requirements: high removal of oils and hydrocarbons, COD reduction.
MITA WT Wastewater treatment tecnologies
- Lamella pack oil separators: effective for the primary separation of free oils and hydrocarbons.
- Dissolved Air Flotators (DAF): for a more thorough removal of oils and greases, including emulsified ones (subject to prior breaking of the emulsion).
- Rotating Biological Contactors (Biodiscs): can be used downstream of the oil separation to degrade the biodegradable fraction of the residual hydrocarbons.
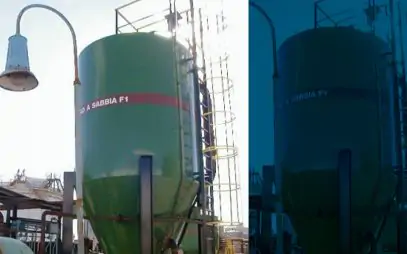
Application: Oil & Gas
Read the article and find out how we can support you5.6. Water Treatment for Chemical and Pharmaceutical Plants
Characteristics of the effluent: extreme variability. Presence of solvents, APIs (Active Pharmaceutical Ingredients), complex organic compounds, high COD, sometimes toxic or inhibitory substances.
Requirements: degradation of specific organic substances, COD reduction, management of variability.
MITA WT Wastewater treatment tecnologies
- Rotating Biological Contactors (Biodiscs): very versatile for treating wastewater with biodegradable organic substances (solvents, alcohols, esters). Their robustness makes them suitable for supporting variations in load and composition typical of multi-product productions. Excluded for industries producing antibiotics, where the bacteria of the biodiscs would be inhibited.
- Tertiary Filtration (Cloth Filters / Sand Filters): for the removal of residual solids or chemical sludges from any pre-treatments.
Important: as in other areas, and perhaps more so than in others, experimentation with a pilot test is absolutely crucial given the complexity and specificity of the wastewater.
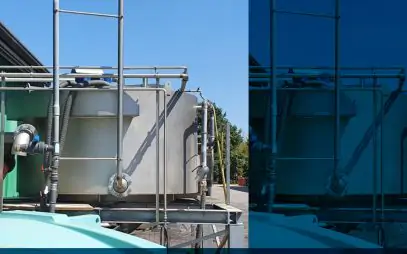
Application: Chemical and Pharmaceutical Plants
Read the article and find out how we can support you5.7. Water Treatment for Paper Mills
Characteristics of the effluent: high presence of cellulose fibers, inorganic fillers, binders, ink residues (from waste paper), COD.
Requirements: fiber recovery, removal of suspended solids, COD reduction.
MITA WT Wastewater treatment tecnologies
- Dissolved Air Flotators (DAF): historically one of the main applications. Used both for the recovery of paper fibers (process machine) and for the treatment of the final effluent (removal of TSS and associated COD).
- Rotating Biological Contactors (Biodiscs): adopted for biological treatment, especially in paper mills with more open cycles (lower COD concentration) or as finishers downstream of other processes. Useful for adaptability to variable loads (e.g. from waste paper).
- Pile Cloth Filters / Continuous Sand Filters: for finishing the effluent and removing the finest solids.

Application: Water Treatment for Paper Mills
Read the article and find out how we can support you5.8. Wastewater Treatment for Mechanical Workshops
Characteristics of the effluent: mainly emulsified and non-emulsified oils, metallic residues, detergents.
Requirements: effective separation of oils.
MITA WT Wastewater treatment tecnologies
- Lamella Pack Oil Separators: an ideal and compact solution for the removal of non-emulsified oils, which are very polluting and can compromise subsequent treatments or discharge. Downstream, if necessary, biological treatments (e.g. Biodiscs) can be provided for the residual organic fraction, or filtration.
5.9. For all sectors: Tertiary Filtration and Water Reuse
Regardless of the sector, discharge regulations are becoming increasingly severe, especially for suspended solids. Furthermore, the growing water scarcity and the associated costs push towards the reuse of treated water.
In these contexts, tertiary filtration is often indispensable.
MITA WT Wastewater treatment tecnologies
- Pile Cloth Media Filters: represent a cutting-edge solution for final polishing. They achieve very high TSS removal yields (often < 5 mg/l), comparable or superior to traditional sand filters, but with significant advantages:
- Continuous filtration even during backwashing.
- Minimal head losses (gravity filtration).
- Reduced energy consumption.
- Extremely contained footprint.
- Ideal for water reuse in agriculture or for non-potable industrial uses.
- Continuous Sand Filters: a robust and reliable alternative for tertiary filtration, with the advantage of continuous self-cleaning.
- Biocombi Compact Plants: for smaller plants or specific needs, this solution integrates biological treatment with biodiscs and final filtration on cloth, offering a high-quality effluent ready for discharge or reuse.
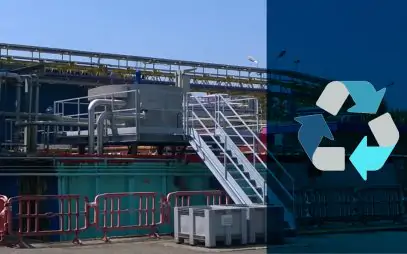
Industrial Wastewater Reuse
Read the article and find out how we can support you6. The MITA Water Technologies Approach: Experience, Innovation and Tailor-made Equipment
As we have repeatedly stated, the treatment of industrial wastewater does not allow for standard solutions. The MITA Water Technologies approach is based on:
- Listening and in-depth analysis: understanding the specific needs of the client, the characteristics of the effluent, the regulatory and operational constraints.
- Technical evaluation and experience: putting to use decades of experience in various industrial sectors.
- Experimentation with a pilot unit: where necessary, we install pilot plants at the client’s site. This allows to:
- Verify the effectiveness of the proposed technologies on the real effluent.
- Collect precise data for the design of the definitive plant.
- Optimize the process parameters.
- Give the client certainty in the technological choice.
- Design and supply of optimized solutions: developing the most suitable plant solution, using our proprietary technologies (biodiscs, cloth filters, sand filters, flotators, etc.) and integrating them, if necessary, with others.
- After-sales support: assistance for start-up, maintenance and continuous optimization of the plant.
Our technological portfolio is designed to offer efficiency, reliability, simplicity of management and low operating costs, fundamental aspects for every industrial reality.
7. In conclusion: to each industry (and to each water) its system
The world of industrial wastewater treatment is constantly evolving: changing regulations, increasingly sophisticated technologies, variability of wastewater… this guide is born from our experience in the field and offers you a clear picture of the challenges, essential parameters and MITA systems.
- Know your effluent. TSS, BOD, COD, nitrogen, phosphorus and specific contaminants: these are the “signals” to be interpreted. Only a detailed analysis — ideally with an on-site pilot system — allows you to choose the optimal treatment path.
- Focus on data, not assumptions. Pilot tests reduce risks and confirm results: it is our road-map for an effective and economical system.
- Turn the challenge into an advantage. A well-designed purification plant is not only regulatory compliance, but also water savings, cost reduction and improvement of CSR.
The next step? Talk to the consultants at MITA Water Technologies. We are ready to analyze your case, assist you in pilot tests and design a “tailor-made” treatment chain for your reality.
8. FAQ – Frequently Asked Questions on Industrial Wastewater Treatment Systems
Below is a collection of frequently asked questions that we receive and that can help to clarify further doubts.
- What is the difference between domestic and industrial wastewater? Domestic (or civil) wastewater comes from homes and services, and has a relatively constant and predictable composition (mainly organic substance, nutrients, solids). Industrial wastewater, on the other hand, derives from production processes and its composition varies enormously depending on the type of industry (e.g. chemical, food, textile, metallurgical), and may contain a wide range of specific pollutants (heavy metals, solvents, oils, extreme pH, high concentrations of COD, etc.) and with very variable loads and flow rates. Precisely because of this heterogeneity, each treatment plant for industrial wastewater is a case in itself.
- What must be removed from industrial wastewater? It depends on the type of industry and the current regulations. Generally, the following are removed: suspended solids (TSS), organic substance (measured as BOD and COD), nutrients (nitrogen and phosphorus), oils and greases, heavy metals, and other specific pollutants from the production process (e.g. colorants, solvents, phenols). The goal is to make the water suitable for discharge into a water body, sewer, or for reuse.
- How is industrial wastewater treated before being discharged? The treatment is a multi-stage process that may include:
- Pre-treatments: Screening, grit removal, oil separation.
- Primary Treatments: Sedimentation or flotation to remove settleable solids and part of the BOD.
- Secondary (Biological) Treatments: Reduction of the biodegradable organic substance (BOD) and, sometimes, nutrients. Examples: activated sludge, rotating biological contactors (MITA biodiscs).
- Tertiary (Polishing) Treatments: Filtration (e.g. MITA sand filters or cloth filters), disinfection, advanced nutrient removal, to meet stricter limits or for reuse.
- Advanced Treatments: For specific or refractory pollutants (e.g. activated carbon, reverse osmosis).
The exact sequence is always customized.
- What are the main types of industrial wastewater treatment? They can be classified into:
- Physical: Sedimentation, flotation, filtration (sand, cloth), screening.
- Chemical: Precipitation (e.g. for metals or phosphorus), neutralization (pH correction), chemical oxidation/reduction, coagulation/flocculation.
- Biological: Processes that use microorganisms to degrade the organic substance (e.g. activated sludge, MITA biodiscs, MBBR).
Often combinations of these methods are used.
- What is the primary treatment of industrial wastewater? The primary treatment aims to remove settleable and floatable suspended solids. Common technologies include decanters (or settlers, such as MITA lamella pack decanters) and flotators (such as MITA DAF dissolved air flotators). This stage reduces the load on subsequent treatments.
- What are the 3 main phases (or stages) of wastewater treatment? Traditionally we speak of:
- Primary Treatment: Physical removal of coarse and settleable solids.
- Secondary Treatment: Biological removal of dissolved organic substance.
- Tertiary Treatment: Further polishing to remove residual solids, nutrients, pathogens, or for reuse purposes.
In industrial wastewater, specific pre-treatments and sometimes advanced treatments are often added.
- What are total suspended solids (TSS)? They are all the solid particles, organic and inorganic, that remain in suspension in the water and do not dissolve. They are measured in milligrams per liter (mg/l) and their removal is one of the primary objectives of the treatment. MITA technologies such as cloth filters and sand filters are very effective in removing TSS.
- How are BOD and COD reduced in wastewater? BOD (biochemical oxygen demand) is mainly reduced with biological treatments (e.g. MITA biodiscs, activated sludge) where microorganisms consume the biodegradable organic substance. COD (chemical oxygen demand) includes both the biodegradable fraction and the non- (or difficult to) biodegradable fraction. The biodegradable part is reduced with biological treatments; for the refractory part, physical-chemical treatments (e.g. chemical oxidation, adsorption) may be necessary.
- Why is the pilot test important in industrial water treatment? Given the extreme variability of industrial wastewater, a pilot test (i.e., the use of a small test plant directly on the company’s wastewater) is crucial to:
- Verify the actual effectiveness of a technology on that specific wastewater.
- Optimize the design parameters (chemical dosages, contact times, etc.).
- Predict the performance of the full-scale plant.
- Reduce the investment risks in non-optimal systems. MITA Water Technologies strongly believes in the approach based on pilot tests.
- What are the advantages of MITA rotating biological contactors (biodiscs)? Biodiscs offer several advantages, especially for industrial wastewater:
- Low energy consumption.
- Simplicity of management and maintenance.
- High resistance to variations in organic and hydraulic load.
- Contained production of excess sludge.
- Modularity and reduced footprint.
- Suitable for treating wastewater with biodegradable substances in various sectors (food, chemical, pharmaceutical – with due exceptions).
- When are MITA cloth filters used? MITA free-fiber cloth filters are ideal for tertiary filtration (final polishing) to:
- Remove residual suspended solids with very high efficiency (up to < 5 mg/l TSS).
- Comply with very strict discharge limits.
- Produce high-quality water suitable for reuse (e.g. irrigation, industrial uses).
- Replace or supplement traditional sand filters, offering advantages in terms of footprint, head losses and backwash management.
They are also used for the removal of microplastics or as part of the MITA Biocombi compact plants.
- What are the MITA Biocombi compact plants? They are “package” systems that integrate in a single compact system the biological treatment with biodiscs and the final filtration on cloth. They are ideal for small and medium-sized industrial users (e.g. food industry, wineries, small communities) that require a complete and efficient treatment in limited spaces and with simplified management.
- How are oils and greases removed from industrial wastewater? The removal depends on the form in which they are present:
- Free and floating oils: Gravity separators (e.g. API/CPI MITA lamella pack oil separators).
- Finely dispersed or emulsified oils and greases: MITA Dissolved Air Flotators (DAF), often preceded by coagulation/flocculation to break the emulsions.
For very stable emulsions or dissolved oils, more advanced technologies may be needed.
- Does MITA Water Technologies offer all the technologies for the treatment of industrial wastewater? MITA Water Technologies offers a wide portfolio of consolidated and efficient technologies, such as rotating biological contactors (biodiscs), cloth filters, continuous sand filters, dissolved air flotators (DAF), lamella pack decanters, oil separators and Biocombi compact plants. However, the field of industrial wastewater treatment is vast. Our philosophy is to propose the most suitable systems based on our experience and our range of products, always emphasizing that each effluent is unique and requires a specific analysis, often with a pilot test, to define the best treatment chain, which could also include complementary technologies.
- What is first flush rainwater and how is it treated? First flush rainwater is that which, during a weather event, washes away impermeable surfaces (yards, roofs), dragging with it the accumulated pollutants (oils, dust, debris). In industrial settlements, it can contain specific substances related to the activity. The treatment typically includes:
- Separation of suspended solids.
- Oil separation (e.g. with MITA lamella oil separators) if there is a risk of hydrocarbon contamination.
- Sedimentation/filtration for fine solids.
- Any specific treatments depending on the type of pollutant.
There are regulations that govern the management and disposal of first flush rainwater.
Resources
Needs of wastewater treatment
Discover the solution for all needsComparing different technologies
Find out all the different technologiesFind out more
All technical articlesOur Newsletter
Sign up for the MITA Water Technologies newsletter: stay up-to-date on systems for municipal and industrial wastewater treatment and filtration.